Vibration testing equipment plays a vital role in ensuring the reliability and performance of various products and systems. From aerospace components to consumer electronics, the need for accurate and reliable vibration testing has never been higher.
In this comprehensive guide, we will explore the latest advancements in vibration testing equipment, as well as key considerations when selecting the right tools for your testing needs. Whether you are a seasoned engineer looking to upgrade your testing capabilities or a newcomer to the world of vibration testing, this guide will provide valuable insights to help you shake up your standards and elevate your testing protocols.
Key Features and Considerations for Vibration Testing Equipment
When selecting vibration testing equipment, it is important to consider key features that will ensure accurate and reliable results. Some crucial considerations include the frequency range of the equipment, as different applications may require testing at specific frequencies.
Additionally, the amplitude range of the equipment will determine the maximum level of vibration that can be applied. It is also important to consider the type of sensors and transducers used in the equipment, as well as the overall quality and durability of the components.
Calibration and maintenance requirements should also be taken into account to ensure the equipment remains in optimal working condition. By carefully considering these key features, you can choose the right vibration testing equipment for your specific needs.
Selecting the Right Vibration Testing Equipment for Your Needs
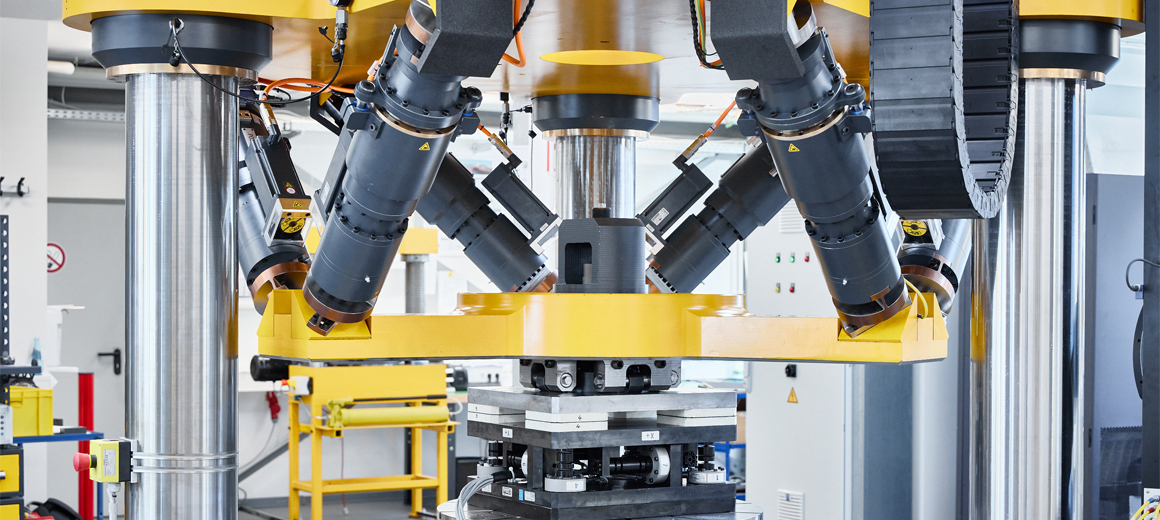
Choosing the right vibration testing equipment for your specific needs can be a daunting task, with a myriad of options available on the market. Factors such as frequency range, amplitude, and testing environment must all be taken into consideration to ensure accurate and reliable results.
Whether you are conducting research and development, quality control, or production testing, selecting the appropriate equipment is essential for achieving the desired outcomes. By carefully evaluating your requirements and comparing the features of various systems, you can make an informed decision that will meet your testing objectives effectively.
Best Practices for Conducting Vibration Testing
Best practices for conducting vibration testing include ensuring proper equipment setup and calibration, selecting appropriate test levels for the specific application, and conducting thorough data analysis and interpretation. Before beginning any testing, it is essential to calibrate the vibration equipment to ensure accurate and reliable results.
Additionally, choosing the correct test levels based on the intended use of the product is crucial for obtaining relevant data. After completing the testing, it is important to analyze the results comprehensively to draw meaningful conclusions and make informed decisions.
By following these best practices, companies can ensure the success of their vibration testing processes and ultimately improve product quality and reliability.
Maintenance and Calibration of Vibration Testing Equipment

Ensuring the proper maintenance and calibration of vibration testing equipment is paramount in guaranteeing accurate and reliable test results. Regular calibration checks should be conducted to ensure that the equipment is operating within its specified parameters.
This includes verifying the accuracy of accelerometers, shakers, and data acquisition systems. In addition, routine maintenance tasks such as cleaning, lubricating, and inspecting components should be carried out to prevent any potential issues that could affect the performance of the equipment.
By staying on top of maintenance and calibration, users can have confidence in the consistency and accuracy of their vibration testing results, ultimately leading to more reliable and meaningful data analysis.
Case Studies: Real-World Applications of Vibration Testing Equipment
Case studies provide real-world examples of how vibration testing equipment is utilized in various industries. For instance, a leading automotive manufacturer used vibration testing equipment to ensure the reliability of their vehicles by subjecting them to intense vibration tests to simulate real-world driving conditions.
In another case, a major aerospace company utilized vibration testing equipment to assess the structural integrity of their aircraft components, ultimately improving the safety and performance of their fleet. These examples demonstrate the diverse applications of vibration testing equipment across different sectors, highlighting its importance in ensuring product quality and reliability.
Future Trends in Vibration Testing Technology

The future of vibration testing technology is set to be revolutionized by advancements in artificial intelligence and machine learning algorithms, allowing for more precise and efficient testing processes. With the integration of smart sensors and advanced data analytics, vibration testing equipment will be able to automatically identify potential failure points and provide real-time feedback for enhanced predictive maintenance strategies.
Additionally, innovations in materials and design will result in more compact and mobile testing devices, allowing for on-the-go testing in a variety of environments. These trends point towards a future where vibration testing equipment is not only more accurate but also more accessible and user-friendly for a wider range of industries and applications.
Conclusion
In conclusion, vibration testing equipment plays a crucial role in ensuring the quality, safety, and reliability of products in various industries. By investing in high-quality equipment and following best practices, companies can effectively assess the performance and durability of their products under real-world conditions.
With an understanding of the essential guide to vibration testing equipment, businesses can enhance their testing processes, improve product quality, and ultimately gain a competitive edge in the market.